Technology Meets Luxury: Looking Back at Dior’s Breakthrough in Footwear Manufacturing
- Nader Alk
- Mar 20
- 3 min read
Dior unveiled its Derby shoes and boots during Paris Fashion Week as part of their Fall/Winter 2023 collection, a hallmark moment in highlighting the brand’s continuous advancements in luxury fashion. Here we are taking a look deeper at what happened behind the scenes.
These footwear pieces incorporated 3D printing technology, advanced materials, and optimized manufacturing processes to enhance structural stability, durability, and production efficiency. But how exactly is this innovative technology applied in terms of craftsmanship and materials?
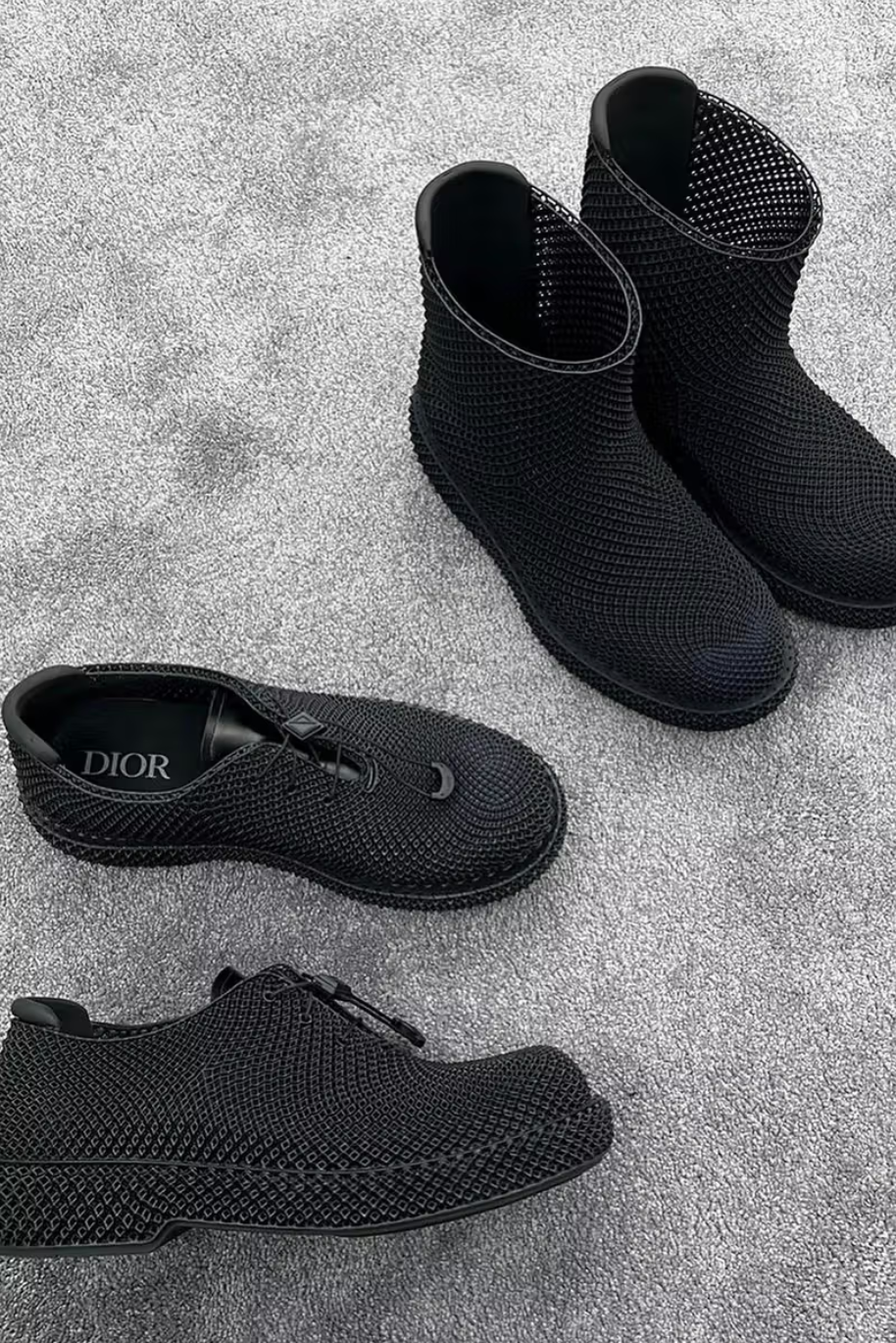
Precision Control and Efficient Production
Dior employs Laser Powder Bed Fusion (LPBF), a high-precision 3D printing technique that uses powdered materials, selectively melting them layer by layer with a laser to form the final shoe structure.
The production process begins with a 3D scan of the classic Carlo Derby shoe, allowing the design team to refine the digital model using advanced modeling software. This optimization ensures the final product is lightweight while maintaining strong structural support. During the design phase, topology optimization algorithms are used to minimize material waste while enhancing overall durability.
During the printing stage, Dior utilizes PA11 (nylon 11) powder, a bio-based nylon material that is both flexible and highly durable. Once the layers are fused together, the resulting shoe upper is lightweight yet structurally robust.
Still, simply producing the shoe through printing does not suffice. Ensuring the final product meets Dior’s high-quality standards is equally crucial. To achieve this, Dior has developed a comprehensive post-processing system. After printing, the excess powder is removed through airflow or vibration-based depowering techniques. Next, the shoes undergo heat treatment at high temperatures to enhance material strength and durability. Finally, a special coating treatment is applied to the surface to improve water resistance, and wear resistance, and provide a refined finish.
High-Performance Materials with Sustainability in Mind
Innovations in 3D printing manufacturing would not be possible without advances in materials, and Dior has made a strategic shift in material selection. The brand has chosen PA11, a bio-based polymer derived from castor oil, which is more environmentally friendly than traditional synthetic plastics. This material offers exceptional flexibility and impact resistance, making the footwear more durable.
Compared to PA12 (nylon 12) - a semi-crystalline thermoplastic known for low water absorption, excellent dimensional stability, and chemical resistance - PA11 provides greater abrasion resistance while also supporting more sustainable manufacturing processes due to its natural origins.
However, relying on just one material cannot fully address the varied demands of high-end footwear. To further enhance comfort and functionality, Dior is also experimenting with high-performance thermoplastic polyurethane (TPU) for the sole structure. TPU offers exceptional elasticity and shock absorption, allowing the sole to adapt to various surfaces for improved wearability. The combination of these materials achieves an optimal balance of lightweight design, durability, and sustainability.

Enhancing Comfort Through Precision Engineering
Throughout the manufacturing process, Dior has meticulously adjusted structural densities for different areas of the shoe. High-pressure areas, such as the sole and toe cap, have increased fill density to improve abrasion resistance and impact protection, while the upper part of the shoe has a reduced density to minimize weight and improve flexibility. Additionally, the shoe's last design has been optimized to provide a more ergonomic fit and superior comfort for wearers.
One of the most significant improvements in this process is seamless integration. Unlike traditional footwear, which requires adhesives or stitching, Dior’s 3D-printed shoes are created in a single-piece structure, eliminating weak points caused by material aging and adhesive degradation. This approach enhances durability while reducing material waste, further supporting sustainable fashion production.
What’s Next for Dior’s Innovation?
By integrating 3D printing, high-performance materials, and smart manufacturing techniques, Dior is reshaping perceptions of luxury footwear production. However, this technology is still in its early stages. Will it truly revolutionize large-scale manufacturing? That remains an open question.
Perhaps the brand will continue refining material sustainability, experiment with more durable polymer compounds, or invest in personalized customization. Meanwhile, will other luxury brands follow Dior’s lead and bring digital manufacturing to the high-end footwear market? These questions are worth watching.
Dior’s 3D-printed footwear is not just a demonstration of technological progress; it marks the beginning of a new era in luxury craftsmanship. While it may not completely replace traditional shoemaking, this shift towards digitized, precision-driven manufacturing signals a potential new standard for high-end fashion production.
Sources: hypebeast.com | designboom.com | weerg.com | xometry.pro
Images: hypebeast.com
Comments